Pharmaceutical production plants rely on various organic solvents during drug manufacturing. As solvent costs continue to rise, recovering and reusing these solvents has become essential for maintaining profitability and operational efficiency.
RCM Thermal Kinetics supports pharmaceutical companies at every stage of plant expansion, particularly in distillation and evaporation technologies. Our expertise ensures efficient solvent recovery, reduced waste, and improved sustainability.
Key Phases of Process Development
- Early-Stage Planning & Lab Testing During initial project planning, our distillation and evaporation lab provides critical insights for pharmaceutical R&D teams. By testing process variables on a small scale, we help de-risk full-scale production and optimize efficiency.
- Process Design & Engineering Our engineers work closely with clients to design solvent recovery and evaporation systems that maximize energy efficiency. A well-defined design phase minimizes risks and ensures cost predictability for new production processes.
- RFQ & System Procurement While our greatest value comes during early-stage design, we also provide competitive and innovative solutions at the RFQ stage. Our unique engineering approach enhances energy efficiency and lowers operational costs.
Solvent Recovery & Evaporation in Pharmaceutical Manufacturing
Solvent recovery plays a vital role in pharmaceutical, chemical, petrochemical, and medical device manufacturing. By reclaiming solvents, plants reduce waste disposal costs and minimize raw material expenses.
The Solvent Recovery Process
Common solvents recovered in pharmaceutical production include acetone, isopropanol, methanol, ethanol, and hexane. The distillation process typically involves a two-section column:
- Stripping Section – Separates water from the organic solvent.
- Rectification Section – Concentrates and purifies the solvent for reuse.
While single-solvent recovery can be modeled using simulation software like ChemCad and HYSYS, most pharmaceutical processes involve multicomponent solvent mixtures, requiring advanced expertise to ensure effective separation.
Multicomponent Solvent Recovery
When multiple organic solvents are present, recovery becomes more complex. Vapor-liquid equilibrium data guides the initial separation process, but real-world variations require lab testing to refine system performance. By integrating empirical lab data into process simulations, we create validated, scalable designs that eliminate uncertainties before full-scale implementation.
At RCM Thermal Kinetics, our Continuous Distillation Laboratory provides both short-term and long-term testing, ensuring reliable scale-up to production systems. Our modular glass lab equipment mirrors real-world production conditions, allowing us to fine-tune system performance before implementation.
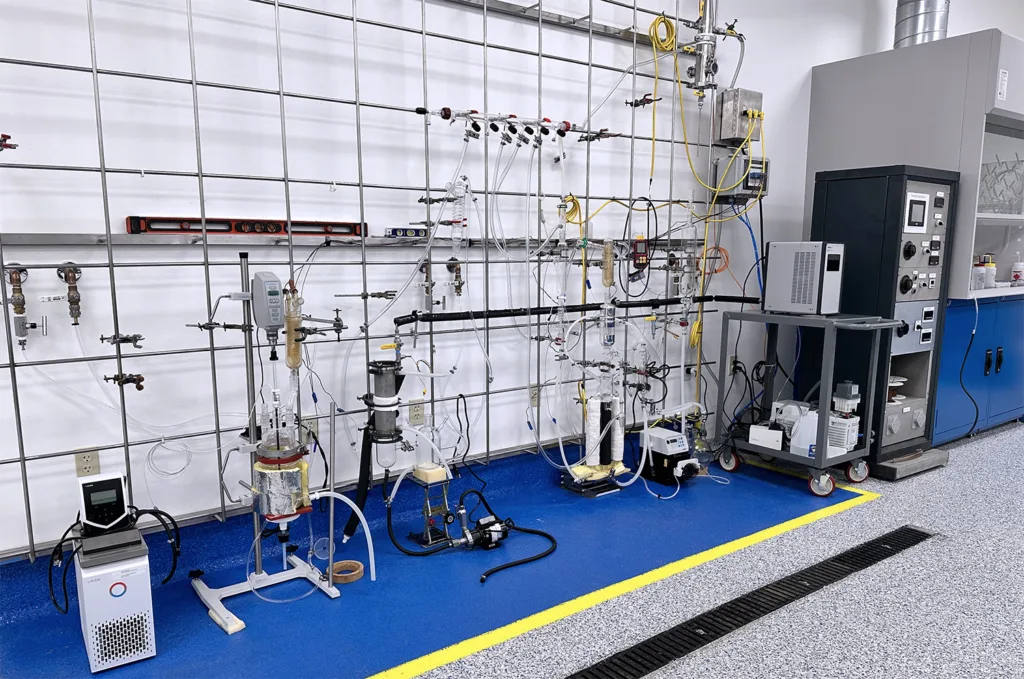
Challenges in Solvent Recovery
Many pharmaceutical plants operate multiple production lines using different organic solvents. A well-designed solvent recovery system must accommodate varying boiling points, multicomponent mixtures, and differing solubility properties.
For example, one pharmaceutical plant handled waste solvent streams with boiling points both above and below water. Additionally, some solvents were miscible when rectified, while others were immiscible. To address this complexity, our engineers:
- Conducted advanced simulations and lab testing to determine optimal separation conditions.
- Designed a distillation column with multiple feed points for precise solvent recovery.
- Implemented a three-phase decanter to separate immiscible and miscible solvent streams efficiently.
Following successful pilot testing, we scaled the system into full production, ensuring seamless integration and optimal energy usage.
Full-Scale System Design & Modular Construction
After lab validation, full-scale system design begins. We specialize in modular construction, which accelerates project timelines and reduces costs. Modular systems offer:
- Faster installation and startup.
- Pre-tested, pre-configured solutions.
- Streamlined logistics and onsite setup.
Manufactured in Buffalo, NY, our modular equipment undergoes rigorous quality testing before shipment. Customers can visit our facility to review progress and ensure specifications align with project goals. Once complete, the system arrives onsite, ready for immediate installation and integration.
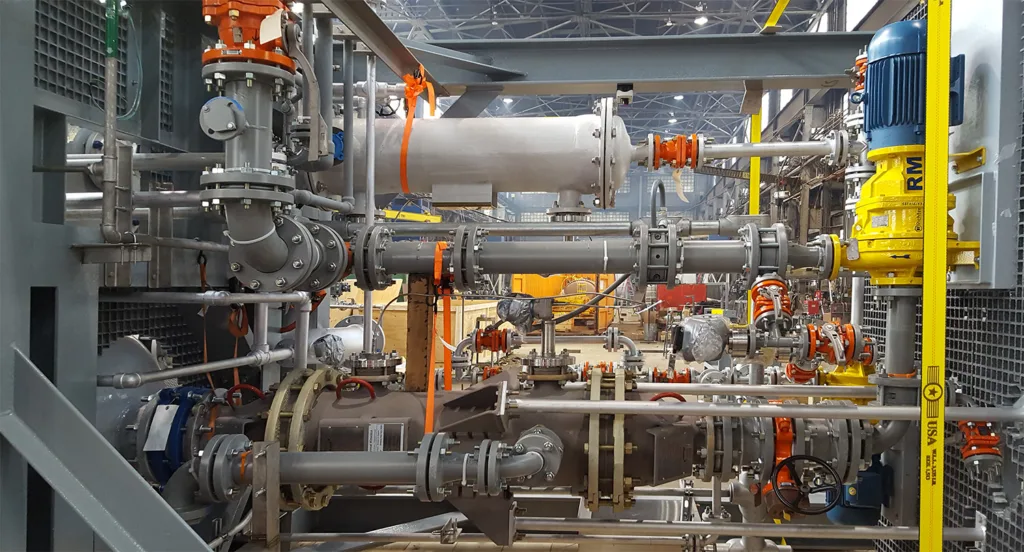
Conclusion
Solvent recovery systems are critical to pharmaceutical production efficiency. However, energy consumption remains a key concern. Our engineers incorporate energy-saving solutions such as:
- Multi-Effect Distillation – Cascading pressure reduces energy demand.
- Mechanical Vapor Recompression (MVR) – Recycles heat to optimize efficiency.
Choosing the right solvent recovery technology requires careful consideration of energy costs, system flexibility, and long-term sustainability. At RCM Thermal Kinetics, we leverage decades of expertise to deliver custom-engineered solutions that enhance performance, lower costs, and drive innovation in pharmaceutical manufacturing.
To learn how RCM Thermal Kinetics can help your facility optimize solvent recovery to maximize profitability and operational efficiency , contact us today.