Crystallization Equipment
RCM Thermal Kinetics designs and manufactures industrial crystallizers, covering inorganic salts, precipitates, and a wide range of industrial chemicals.

Crystallization Processing
Crystallization is the separation process by which heat and mass transfer remove solids from a solution in the form of high purity crystalline structures. The two-part process of associated nucleation and crystal growth depends upon the relative rate of each step to control crystal size and population.
Found in a variety of process and waste management operations, crystallization also reduces liquid waste run-off, as the remaining liquid — also purified — can then be cycled back through the system, released into the environment, or passed on to another operation.
thermal kinetics
Optimizing Crystallization Systems
To achieve optimum efficiency, each crystallization system is designed on an individual basis, as different types of equipment are more suitable for different applications. This differentiation largely depends on the substances in the mixture, the amount of energy input, and desired crystal size. At RCM Thermal Kinetics, our team of engineers, developers, and designers can construct a wide array of custom crystallization equipment to match your unique needs. Whether your crystallizer is a standalone system or part of a larger operation, we can configure it to fit any industry application. From circulating batch models to continuous crystallizers, each of our systems can be adjusted to meet your operational requirements.
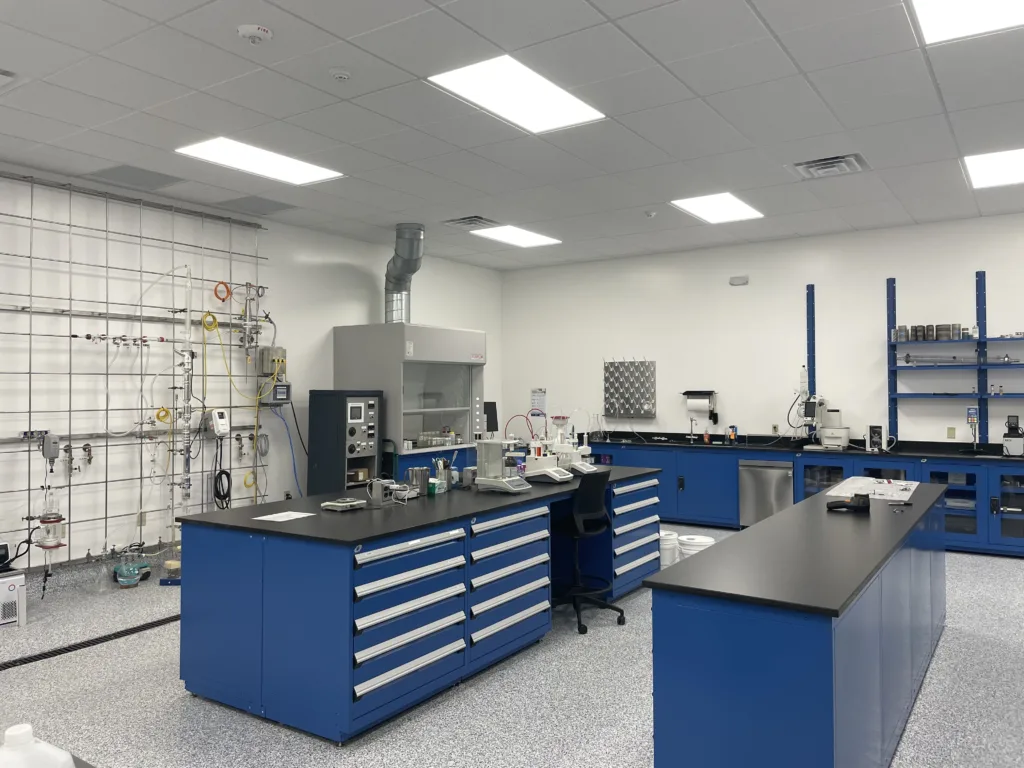
Evaporator Crystallizers
Evaporative crystallization increases the solution concentration by evaporating the solvent. As the concentration increases, the solution becomes supersaturated and nucleation begins. Upon further concentration, the nuclei begin to grow and distinct crystals appear. RCM Thermal Kinetics offers two main styles of evaporative crystallizers, each available with customization options:
A continuous vacuum evaporating crystallizer utilizes a low-speed propeller to direct the mixture upward through a draft tube toward the boiling surface. A small degree of supercooling minimizes the buildup of crystals on the walls, while the remaining liquid flows back downward through the draft tube. This crystallizer is useful for small capacity applications with moderate control of crystal size. Crystal size and size uniformity depend on external separation, fines destruction, and crystal population control.
A circulating batch crystallizer in which, if using external circulation, the solution is pumped through heat exchanger tubes at a high velocity, allows minimal crystal formation on the tubes. If using internal circulation, the solution is pushed by a propeller through a draft tube to circulate internally while a hot feed supplies evaporation energy. Both versions require agitation or circulation to ensure small, pure crystal formation. This type of crystallizer is useful for larger capacities with the same external control of size and size uniformity.
Cooling Crystallization
Cooling crystallization, the process of crystallizing solutions based on solubility temperature dependence, is conducted through indirect heat transfer or directly under vacuum. These methods cause some of the solution to evaporate and then cool to a temperature in equilibrium with the reduced pressure. In essence, a small amount of the solvent flashes off the latent heat, subsequently lowering the temperature of the solution. While this process does cause a reduction in solvent, the crystallization is mainly due to the change in temperature of the solution. Decreasing the temperature supersaturates the solution, developing the nuclei and encouraging crystal growth to force the salt out of solution and crystallize. The cooling crystallization process is performed using one of three systems: vacuum cooling crystallizers, continuous cooling crystallizers, or scraped surface crystallizers.
Useful for maintaining tighter control of crystal size, this operation utilizes either a batch or continuous vacuum process. Batch operation is optimal for controlled crystal sizing, as each crystal endures the process for the same amount of time, leading to consistent dimensions. Continuous operation is optimal for applications where precise control over the crystallization process, high purity of the final product, and efficiency are essential requirements.
This model removes a slurry to a centrifuge, returns centrifuged dilute solution to an evaporator for concentration, and then supplies this concentrated warm solution to the cooling crystallizer.
Once its chilled, vessel walls cause the solution to crystallize on the wall surface. This model uses rotating blades against the walls to dislodge the formed crystals. Once collected, the crystals are returned back to the bulk solution for growth and ultimate extraction as a slurry for further separation in a centrifuge.
thermal kinetics
Full Service Crystallizer Support
Thermal Kinetics supplies the supporting equipment that goes with each crystallizer option. This includes centrifuges to separate the crystals from the saturated solution, splitter boxes/vessels for fines control and destruction, and control valves for the process, pumps, tanks, and instrumentation. Hydroclones are often employed to aid in the control of crystal size, return of fines to the crystallizer, and thicken the slurry prior to centrifuging.
We also offer modular system design and support, allowing for the pre-assembly of all components on a modular skid package for off-site manufacture and seamless on-site installation. Equipped with a database of prior crystallization projects to inspire design approaches and applications, along with testing facilities to gather physical data on your crystallization, the Thermal Kinetics team is well positioned to support your process needs.
This is especially useful for proprietary and specialty chemicals for which solubility data is not readily available, or for a solution of various chemicals which affects the solubility of involved salts.
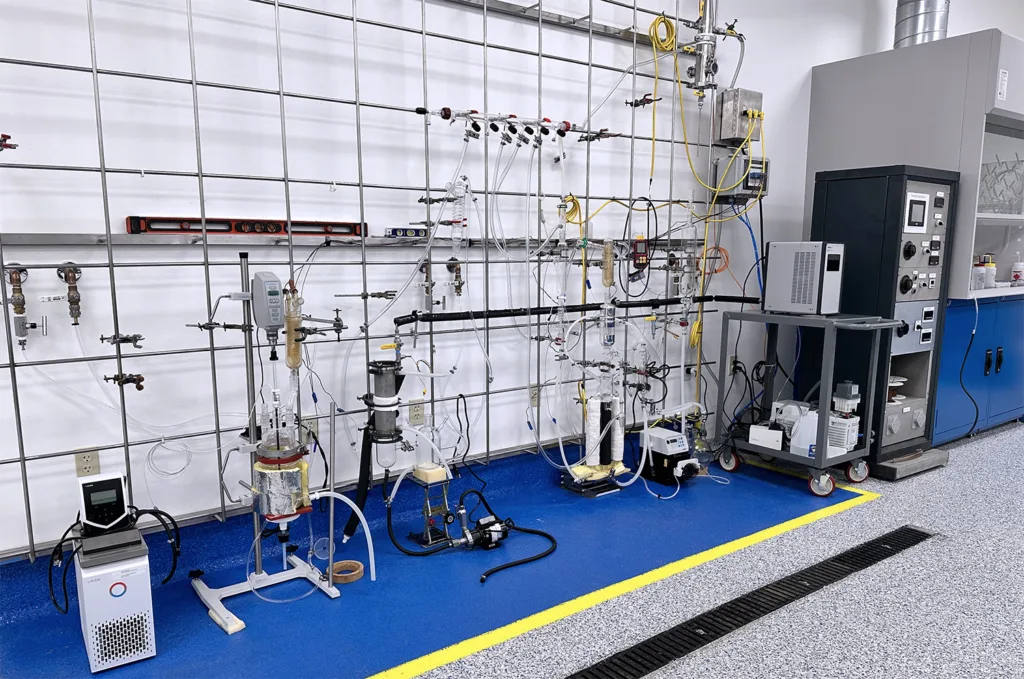
Equipment & Design Capabilities
By using a single supplier to engineer, procure, and assemble the modular system, clients enjoy:
- Shorter production schedule
- Improved quality control
- Cost Savings
- Enhanced safety during construction
- Minimal site disruption
To learn more about how our crystallization equipment and design capabilities can assist in your next project, contact a member of the RCM Thermal Kinetics team today.
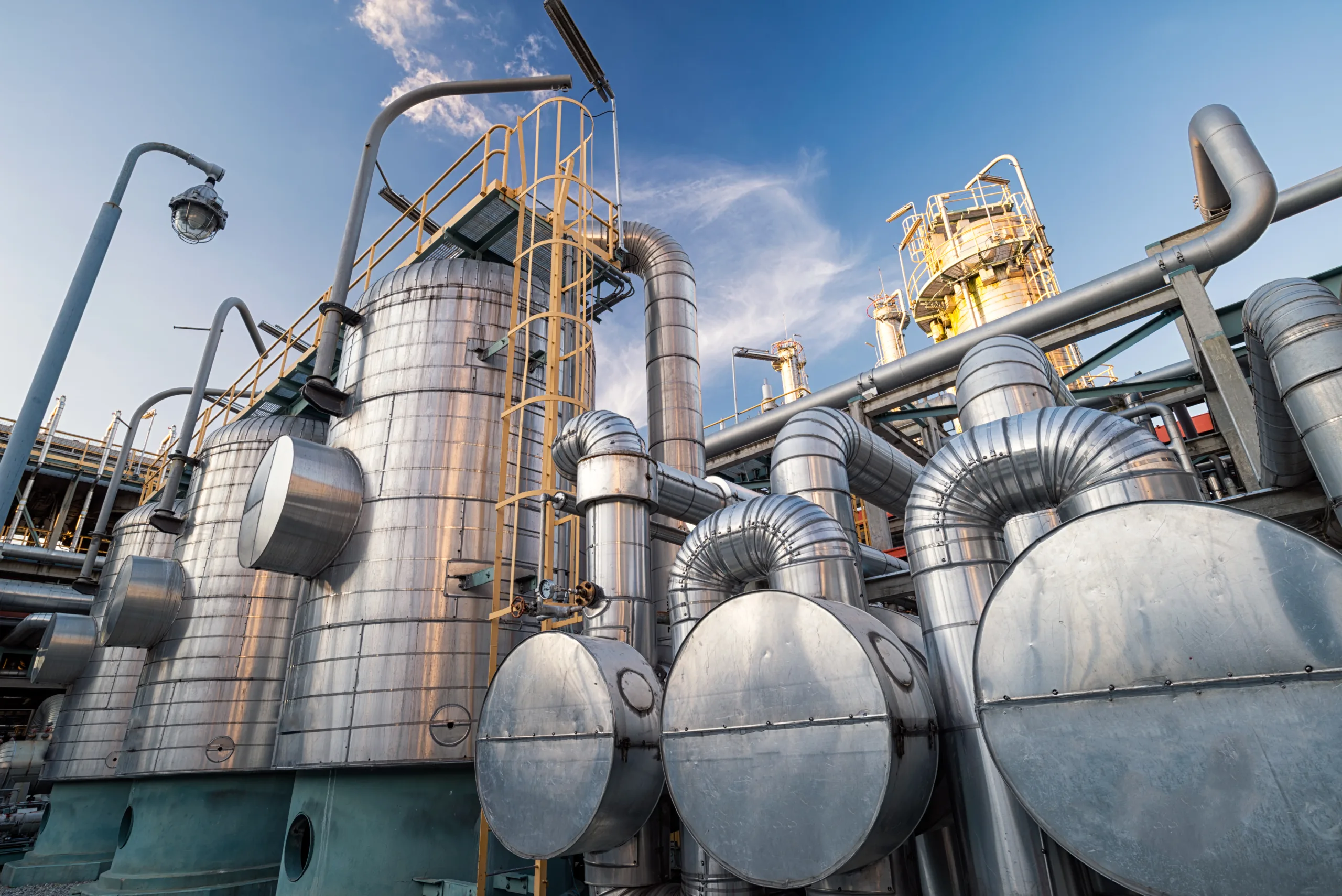
Let’s Collaborate on Scientific Success
Learn more about our customer product and process development activities in our Testing Facility.